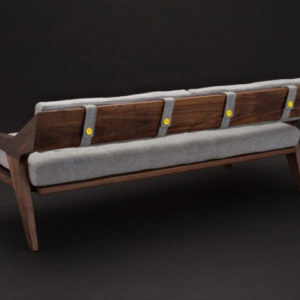
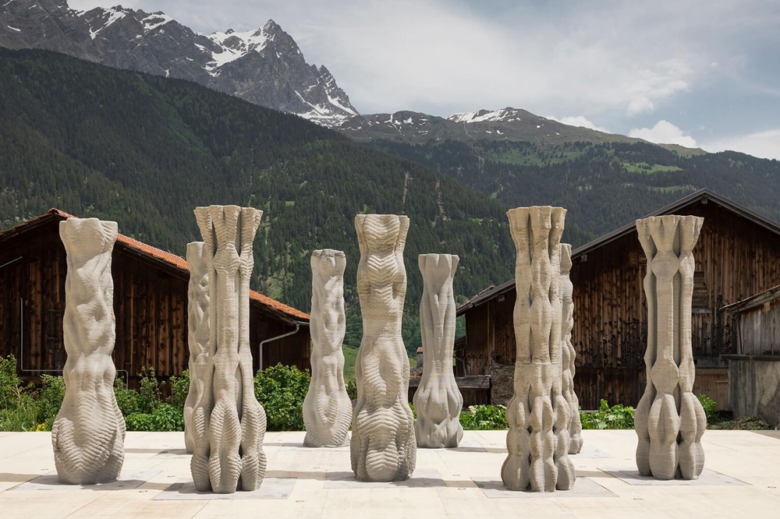
Nearly a decade ago, there were the 3D-printed scale models that Broadway set designers were using to visualize their stage productions. Then there were the first 3D-printed full-scale scenography components, with the likes of Daniel Auber’s production of Fra Diavolo at the Teatro dell’Opera di Roma in 2017. And now, 3D-printed concrete has made it to the dance stage, with a set of bespoke columns for the Origen Festival in Switzerland.
Origen’s winter showcases take place inside a renovated medieval castle, but its summer programme is on display in a theatre made along with nature: the walls of its open-air theatre are made of the Alps that envelop Riom, a bucolic village located an hour away from St. Moritz. There, nine intricately twisted columns, each nearly three metres high, emerge from the platform.
Titled Concrete Choreography, the pieces were devised, designed and manufactured by the students of ETH Zurich’s Master of Advanced Studies in Digital Fabrication and Architecture, using robotic printing. The process allowed them to produce these elements without the need for formwork – they were printed hollow, with filling used strategically. Each one features a one-of-a-kind design and can be produced in full height in less than three hours.
‘Computationally designed material ornament and surface texture exemplify the versatility and significant aesthetic potential of 3D concrete printing when used in large-scale structures,’ said Benjamin Dillenburger, the ETH professor who oversaw the installation. ‘Framing and informing the dance performers of the summer season in Riom, the project demonstrates how technological advancements can bring efficient and novel expressions to concrete architecture.’
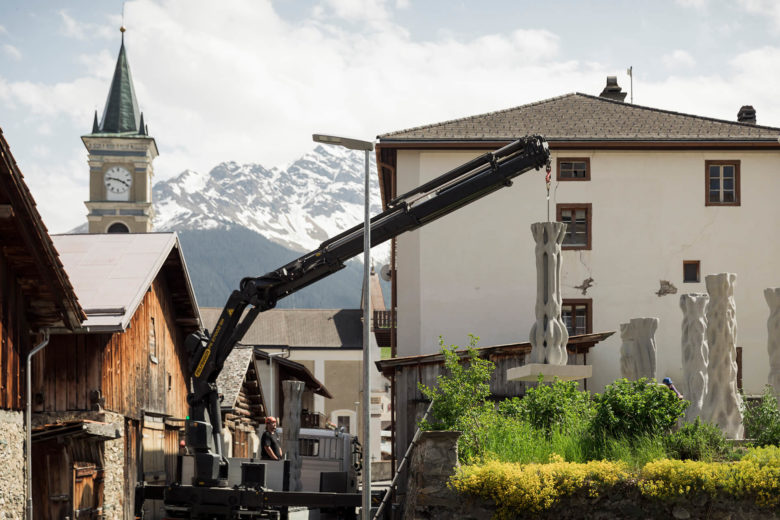
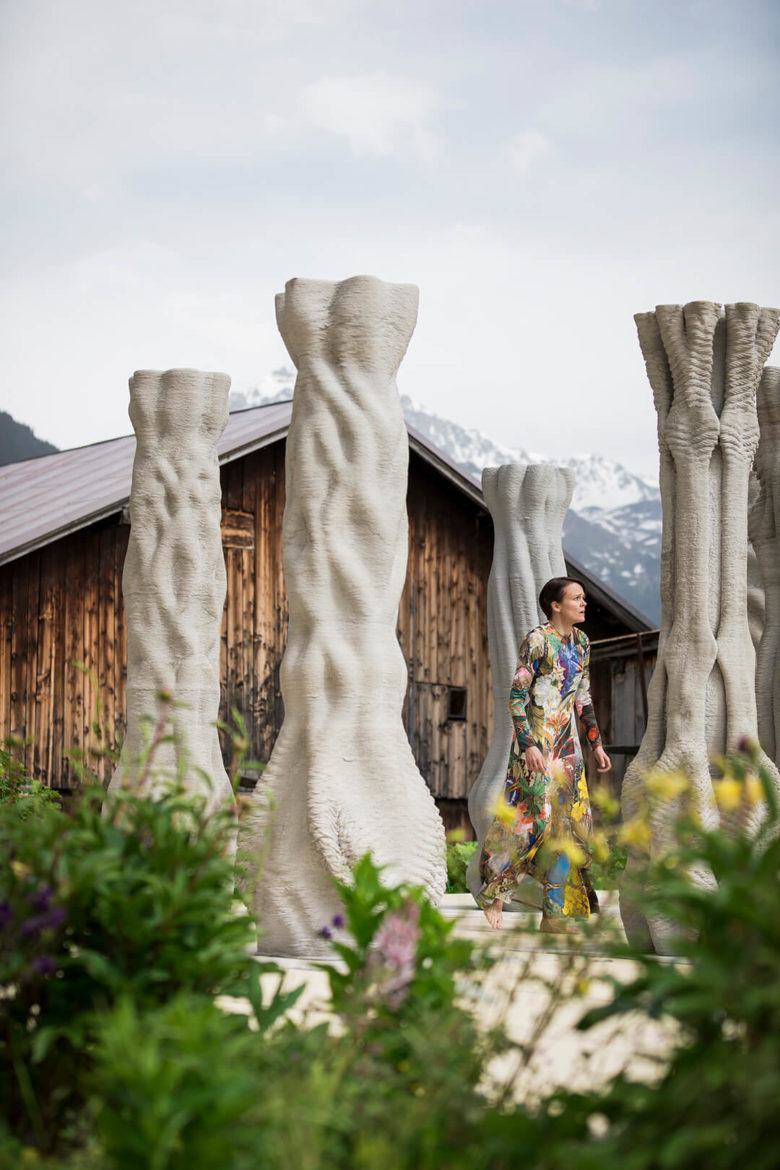
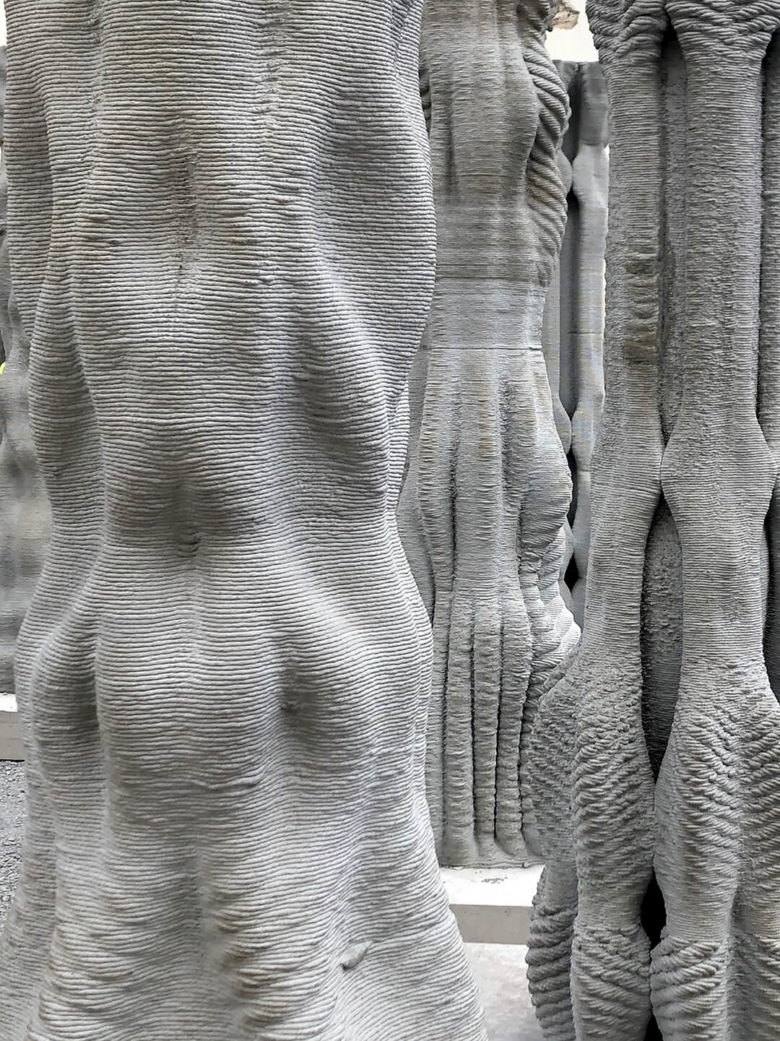
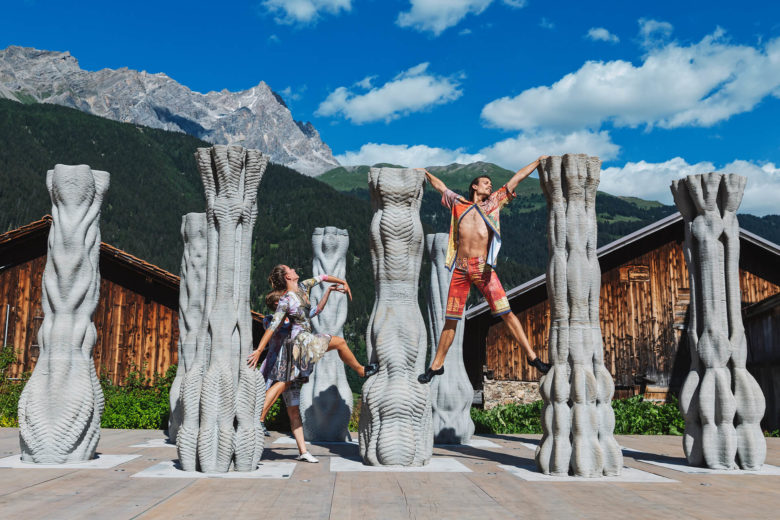
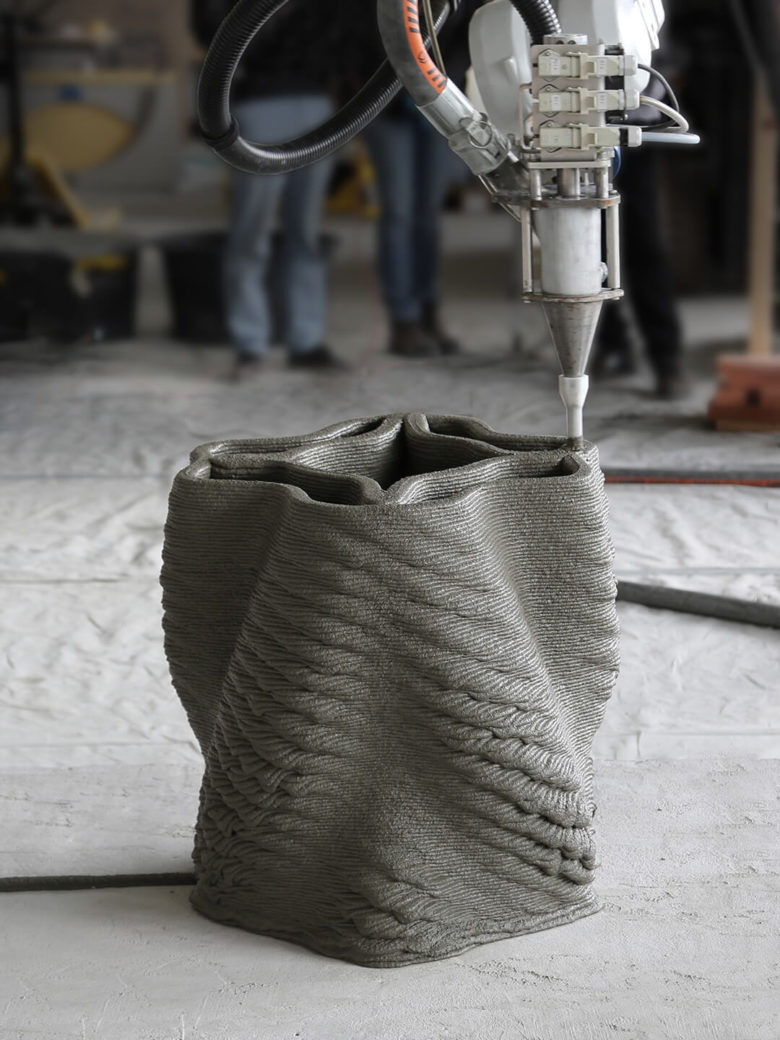