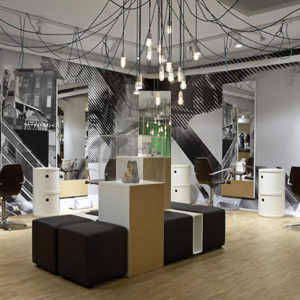

Since the outbreak of COVID-19 many architects and designers have joined the effort to fight the pandemic. With a number of studios utilizing their 3D printers and laser cutters to produce vital face shields, Foster + Partners has now shared a template for a general-purpose visor that can be cleaned and reused.
Composed of just three pieces, the prototype has been designed with the aim of facilitating quick mass production of the visors. Using a Zund G3 M 2500 cutting machine, or its equivalent, an incredible 217 visors can be cut every hour. The British-based practice hopes that by sharing the templates and material specifications as an open-source resource other studios and manufacturers will be encouraged to use their laser cutting machines to produce the much-needed equipment for those on the front line of COVID-19. The file for digital flatbed cutters and the assembly instructions can be found on the Foster + Partners’ website here.
The templates, which are for digital and laser cutters, offer a quicker turnover than masks produced by 3D printing. Each visor can be cut in under 30 seconds and assembled in under a minute. Alternatively, the face shields be flat-packed and distributed quickly in large quantities. Using their digital flatbed cutter foster + partners has been able to cut and assemble components for 1,000 masks in a single day.
The three components comprise a visor made from 0.5mm optically clear PETG, an interlocking soft PP headband, and a surgical silicone rubber head strap that ties the two together. Due to the increasing deficit of raw materials, the face shields are also designed to be easily disassembled, cleaned, sanitised and reused. Foster +partners are now delivering these prototypes to a number of hospitals in London where they are being tested. The practice is also exploring means of getting the design approved for mass production and use by health workers.
Designed by Foster + Partners
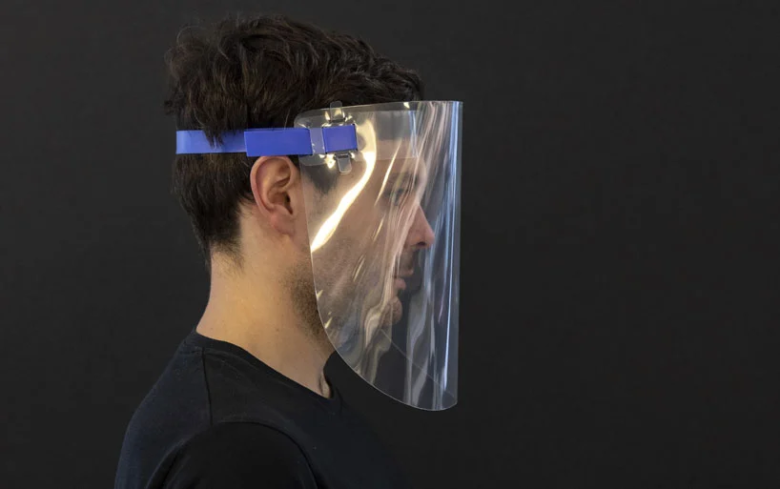
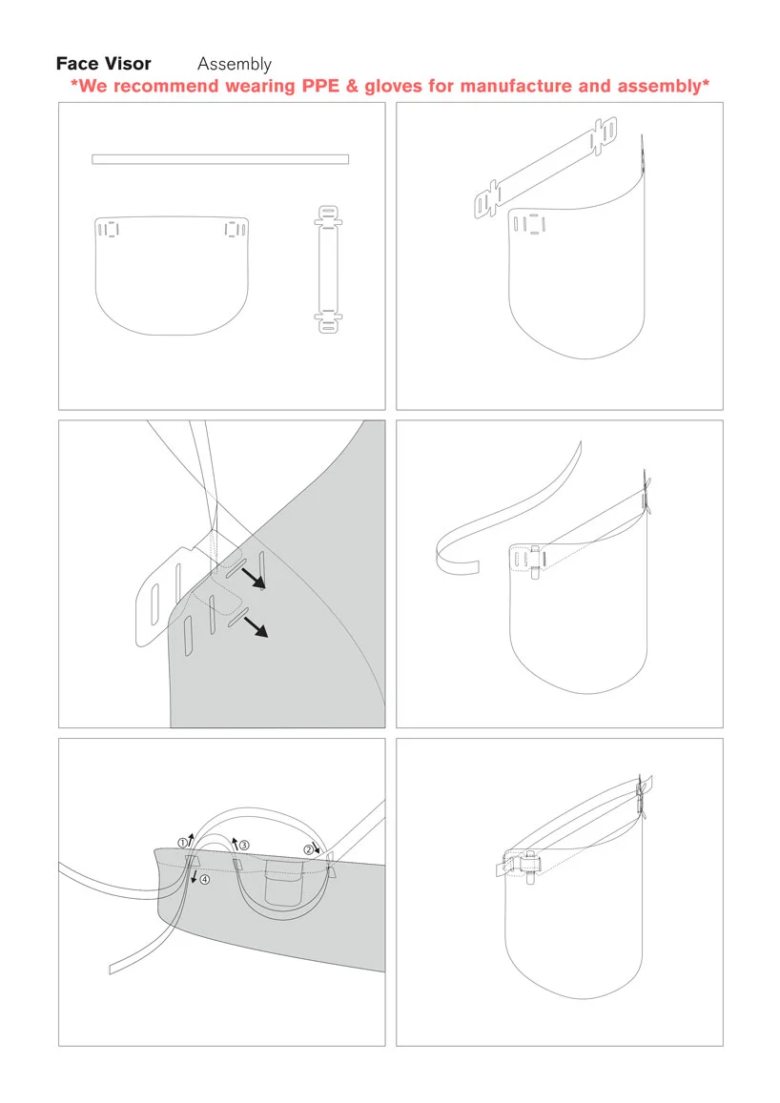
