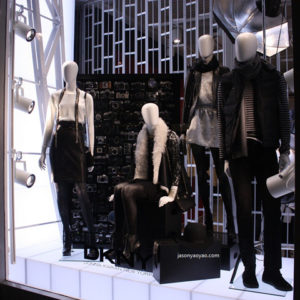

DUS Architects has combined 3D-printed bioplastic with a tensile fabric structure to create a sculptural facade for the building where European Union meetings will take place over the next six months.
The Amsterdam-based studio is currently two years into a project to build the world’s first 3D-printed canal house, so decided to use its pioneering resources to create the facade for the Mobile Europe Building. This temporary structure was built to host the presidency meetings of the EU Council during its six-month period in the Netherlands, before it moves on to Slovakia for the second half of the year. This prompted DUS Architects to create a facade that can be recycled. Tensile fabric structures are commonly used for temporary structures, so the team decided to combine this with their recent research in bio-based 3D-printing filament.
“We’re collaborating with Henkel, a global multinational that does innovative work with materials, and we’re investigating the possibilities to create new printed bio-based printing materials,” explained studio co-founder Hedwig Heinsman. “We’ve developed a special plastic that is entirely bio based, made out of linseed oil,” she told Dezeen. “The advantage of this material is not only that it is made out of plants, but that it can be shredded and reused in the print cycle.”
The fabric structure provides the main shape of the facade – a series of vertical panels that appear to have been lifted up at the base to create triangular openings reminiscent of tent entrances. The intention was for these forms to reference the sailing ships that were historically built in this area. Within these openings, faceted blue surfaces extends out to create benches. These elements were all created using one of two 3D printers involved in the construction of the canal house.
This is the first time in the world that these kinds of “XXL 3D prints” are being shown in the public domain, according to DUS Architects. They were created using fused deposition modelling, the same form of additive manufacturing used by most household 3D printers. “The FDM technique is the most common way of producing small objects, but what we’ve done is scaled up this technique for much larger elements,” explained Heinsman. “We can create elements up to five metres high, two metres wide, and two metres deep” she said.
The Mobile Europe Building was completed in collaboration with building company Heijmans, which is also involved in Daan Roosegaarde’s Smart Highway project and an initiative to build prefabricated starter homes. Other collaborators were parametric developer Actual, temporary structure specialist Neptunus, engineer TenTech and lighting consultant Philips.
It is the first commercial project resulting from the development of the 3D Print Canal House, which is now well underway. Rather than being used as a residence, this building will serve as a “global flagship warehouse” for 3D-printed construction. “The 24-metre-tall building will combine traditional building techniques with XL 3D printed building elements, all related to digitally customisable construction: fully printed rooms, walls, facades, ornamented interiors, etc.” added Heinsman. “The 3D Print Flagship Warehouse will consist of print production areas, workshop areas, a cafe, event space, flex desks, a roof terrace, located on a great waterfront location with amazing views in a booming part of Amsterdam.”
via Dezeen












